making smart prosthetics affordable
​Team [REDACTED]​.
Mechanical Systems.
Our mechanical system consists of several systems, including a feedback cuff, elbow linkage, gripper and actuator, skeleton, and casing with socket. A comprehensive list of materials, costs, CAD models, and descriptions are offered here. The total cost of raw materials for the mechanical system is approximately $68.
A user desires some form of feedback when manipulating objects in the world. More expensive prosthetics can use small electrical shocks to simulate the feeling of lifting. Our design uses a servo to squeeze the top of the arm a proportional amount to what the pressure sensors feel when gripping objects. This is an intuitive way of expressing grip strength because the feeling on the arm and the manipulation being seen correspond directly.
The cuff uses:
-
Micro Servo, $4.95
-
Cloth, $3.00
-
Elastic Band, $2.00
-
Fishing Line, Negligible
-
Metal Belt Hook, $2.00
​Feedback Cuff.​

​Elbow Linkage.​
The elbow linkage is the sensor at the elbow of the user which measures the angle of the arm. This aids in determining the contextual information which controls the prosthetic's actions.
The linkage structure is made from:
-
3D Printed PLA, Negligible



​Gripper and Actuator.​
The prosthetic is outfitted with several 3D printed fingers which will close around objects under the command of the user. The fingers are actuated by a high-torque servo connected to a pulley tree system for relative individual control of each finger. The full grip strength of the system is estimated to be approximately ___N.
This mechanism uses:
-
High Torque Servo, $16.89
-
3D Printed PLA, Negligible
-
Fishing Line, Negligible
-
Blue Spring Steel, $2.50

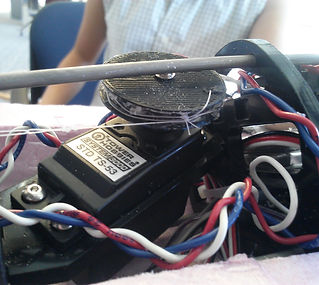

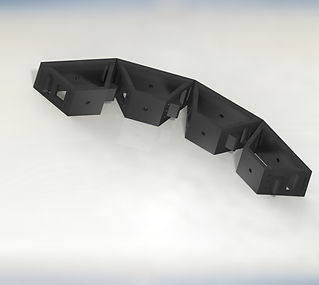
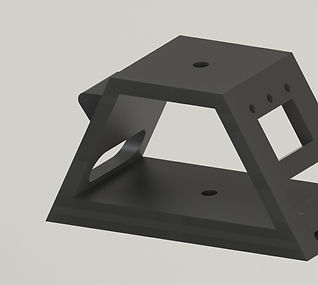

​Skeleton.​
The skeleton is the inner structure of the prosthetic which houses the electronics, and provides the general strength of the arm. This is designed to be lasercut. 1/8" Aluminum rodstock is used to add support and shape to the skeleton.
This structure is made of:
-
Delrin Plastic, $13.12
-
Aluminum Rodstock, $1.39

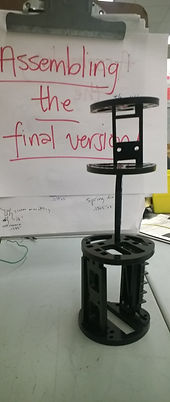
​Socket and Casing.​
The skeleton is a sturdy, breatheable, removable protective shell over the skeleton. It also serves the aesthetic purpose of hiding the innards of the arm. The socket interfaces with the site of ampulation, with an organic shape to conform to the arm and a locking mechanism to enable the user to easily put on or remove the arm. The socket's shape can be changed in CAD to better fit the user.
The casing and socket are:
-
2in Wide Fiberglass Cuff Tape, $11.98
-
Silicone Cups, $17.79 (with shipping)
-
Fabric, velcro, elastic, elmer's glue: negligible
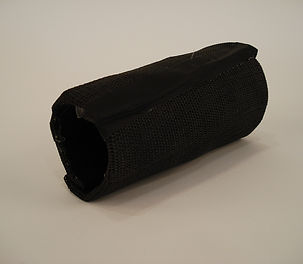
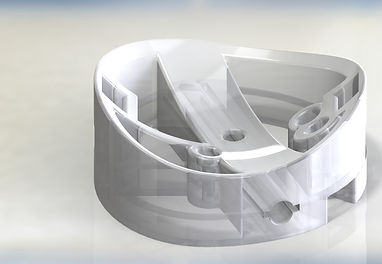

​Putting it Together.​
The mechanical system assembled - in the virtual world and in the physical. After assembling, some of our biggest takeaways are:
-
Tolerancing - even after accounting for measurement error and the fabrication method, we still came up short...or long....or wide...sometimes. The lack of consistency in our fabrication tools caused a lot of post-processing. Accounting for post-processing methods would have saved some time.
-
Electrical Connectors have dimensions - we were able to effectively account for wire routing and volume, but failed to consider that some connectors were wider than the wire, and inflexible.
-
Wire Routing is super important - we kept this in mind throughout, and it played a huge role in some of our design decisions
-
Integration of different mechanical systems requires high-level thinking - towards the end, it would have been great to have an organiztional spreadsheet or flow chart mapping the connections between the mechanical system, attachement methods, fasteners needed, etc so that various members saved time remaking pieces to work with others

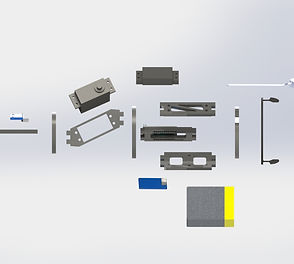

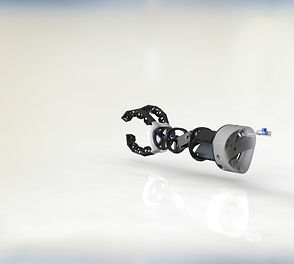
